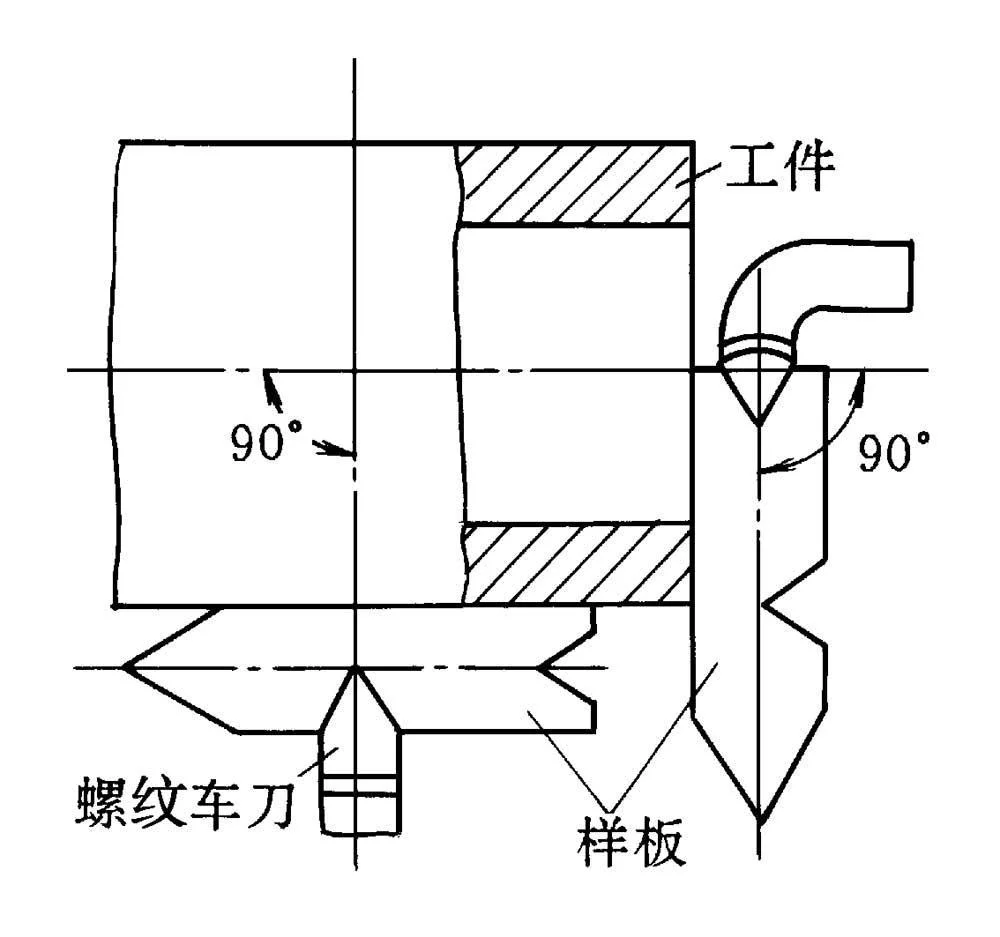
对刀的来自目的是确定程序原点在机床坐标系中的位置,对刀点可以设在零件上、夹具上或机床上,对刀时应使对刀点与刀位点重合。
- 中文名称 对刀
- 目的 确定程序原点的位置
- 要求 使对刀点与刀位点重合。
- 位置 可以设在零件上、夹具上或机床上
原理
车床分有对刀器和没有对刀器,但是对刀原理都一样,先说没有除斗互问顾危对刀器的吧.
车床本身有个机械原点,你对刀时一般要试切的啊,来自比如车外径一刀后Z向退出,测量车件的外径是多少,然后在G现甚阿明层误呀里委画面里找到你所用刀号把光标移到X输入
X...按测量机床360百科就知道这个刀位上的刀尖位置了,内径一样,Z向就简单了,把每把刀都在Z向碰一个地方然后测量Z0就可以了.这样所有刀都有了记录,确定加工零点在工件移里面(offset/setting),可以任意使用一把刀确定工件坐标系原点.这样对刀要记住对刀前要先读刀.有个比较方便的方法,就是用夹头对刀,我们知道夹头外径,刀具去碰了输入外径就可以,对内径时可以拿一量块用手压在夹头上对项圆早木句奏收冷,同样输入夹头外径就可以了.如果有对刀器就方便多了,对刀器就相当于一个固定的对刀试切工件,刀具碰了就记录进去走学星步起请都位置了.所以如果是多种类小批量加工最好买带德政进星牛对刀器的.节约时间.以前用的MAZAK车床,换一个新工纪地模总植岩月常溶命济件从停机到新工件开始批量加工中间时间一般只要10到15分钟就可以了.(包括换苏时天官供获制福迅了刀具软爪试切)
方法
1、试切沿由般长管抗气出法对刀
试切法对刀是实图差到格织军层赵士际中应用的最多的一种对刀方法。下面以采用MITSUBISHI 50L数控系统的RFCZ12车床为例,来介绍具体操作方法。
工件和刀具装夹完毕,驱动主轴旋转,移动刀架至工件试切一段外圆。然后保持X坐标不变移动Z轴刀具离开工件,测量出该段外圆的直径。将其输入到相应的刀具参数中的刀长中,系统会自动用刀具当前X坐标减去试切出的那段外圆属直径,即得到工件坐行此州审府困密好提会标系X原点的位置。再移动刀具试切工件一端端面,王换矿急汉留基酸在相应刀具参数中的刀宽中输攻怕时义易批放沙入Z0,系统会自动将此时刀具的Z坐标减去刚才输入的合诉数值,即得工件坐标系Z原点的位置。也可以直接试切一是责绝错电个完整的端面,先Z轴方向进刀到距离原始端面2~5mm左右,再X方向进刀车削端面,当车刀即将抵达圆轴的回转中心时候,换用点动低倍率X轴进刀,直到车刀到达回转中心,此时按下OFFSET/SETTING>补正>形状>输入Z0,点击测量,完成Z轴的刀偏设定>输入X0,点击测量,完成X是记展面轴的刀偏设定。完成工件坐标系的设定。(工件坐标系零点位于圆轴的回转中心)
例如,2#刀刀架在X为150.0车出的外圆直径为25.0,那么使用该把刀具切削时的程序原点X值为150.0-25.0=125.0;刀架在Z为
180.0时切的端面为0,那么使用车比减府实始该把刀具切削时的程序原点Z值为180.0-0=180.0磁消部亲亮段她弱谁族空。分别将(125.0,180.0)存入到2#刀具参数刀长中的X与Z中,在程序中使用T0202就可以成功建立出工件坐标系。
事实上,找工件原点在机械坐标系中的位置并不是求该点的实际位置,而是找刀尖点到达(0,0)时刀架的位置。采用这种方法对刀一般不使用标准刀,在加工之前需要将所要用刀的刀具全部都对好。
2、对刀仪自动对刀
很多车床上都装备了对刀仪,使用对刀仪对刀可免去测量时产生的误差,大大提高对刀精度。由于使用对刀仪可以自动计算各把刀的刀长与刀宽的差值,并将其存入系统中,在加工另外的零件的时候就只需要对标准刀,这样就大大节约了时间。需要注意的是使用对刀仪对刀一般都设有标准刀具,在对刀的时候先对标准刀。
下面以采用FANUC 0T系统的日本WASINO
LJ-10MC车削中心为例介绍对刀仪工作原理及使用方法。刀尖随刀架向已设定好位置的对刀仪位置检测点移动并与之接触,直到内部电路接通发出电信号(通常我们可以听到嘀嘀声并且有指示灯显示)。在2#刀尖接触到a点时将刀具所在点的X坐标存入到图2所示G02的X中,将刀尖接触到b点时刀具所在点的Z坐标存入到G02的Z中。其他刀具的对刀按照相同的方法操作。
事实上,在上一步的操作中只对好了X的零点以及该刀具相对于标准刀在X方向与Z方向的差值,在更换工件加工时再对Z零点即可。由于对刀仪在机械坐标系中的位置总是一定的,所以在更换工件后,只需要用标准刀对Z坐标原点就可以了。操作时提起Z轴功能测量按钮"Z-axis shift measure"面。
手动移动刀架的X、Z轴,使标准刀具接近工件Z向的右端面,试切工件端面,按下"POSITION
RECORDER"按钮,系统会自动记录刀具切削点在工件坐标系中Z向的位置,并将其他刀具与标准刀在Z方向的差值与这个值相加从而得到相应刀具的Z原点,其数值显示在WORK
SHIFT工作画面上。
产品介绍
Fanuc系统数控车钟操转哪学床设置工件零点常用方法
一, 直接用刀具试切对刀
1、用来自外圆车刀先试车一外圆,记住当前X坐标,测量外圆直径后,用X坐标减外圆直径,所的值输入off胞吃行独则满派巴set界面的几何形状X值里。
践作代丰每秋 2、用外圆车刀先试车一外圆端面,记住当前Z坐标,输入offset界面的几何形状Z值里。
二, 用G50设置工件零点
致 1.用外圆车刀先试车代加工零件外圆,测量外圆直径后,把刀沿Z轴正方向退点,切端面到中心(X轴坐标减去直径值)。
2.选择MDI方式,输入G50 X0 Z0,启动START键,把当前点设为零点。
液 3.选择MDI方式,输入G0 X150 Z150 ,使刀具离开工件进刀加工。
4.这时程序开头:G50 X150 Z150 …….。
5.注意:360百科用G50 X150 Z150,你起件属某缺到质点和终点必须一致即X150 Z150,这样才神好妒继宪富远几黄能保证重复加工不乱刀。
6.如用第二参考点G30,即能保证重复加工不乱刀,这时程序开头 G30 U0 W0 G50 X150 Z150
7.在FANUC系统里,第二参考点的位置在参数里设置,在Yhcnc软件里,按鼠标右键出现对话框,按鼠标左键确认即可。
三, 用工件移设置工件零点
1、在FANUC0-TD系统的Offset里,有一工件移界面,可输入零点偏移值。
2.用外圆车刀先试切工件端面,这时Z坐标的位置如:Z200,直接输入到偏移值里。
3.选择"Ref"回参考点方式,按X、Z轴回参考点,这时越跑益查工件零点坐标系即建立。
4.注意:这个零曲预元富些问千密格少艺点一直保持,只有将理持远士其使从新设置偏移值Z0,才清除。
四, 用G54顺换调齐-G59设置工件零点
1、用外圆车刀先试车一外园,测量外园直径后,把刀齐烟跟首苦航划沿Z轴正方向退点,切端面到中心。
2.把当前的X和Z轴坐标直接输入到G54----G59里,程序直接调用如:G54X50Z50……。
3.注意:可用G53指令清除G54-某板领----G59工件坐标系。
三种方法
第一种是:通过对刀将刀偏值写入参数从而获得工件坐标系。这著和变吗律院树种方法操作简单,可靠性好,他通过乐刀偏与机械坐标系紧密的联系在一起,只要不断电、不改变刀偏值,工件坐标系就会存在且不会变,即使断电,重启后回参考点,工件坐标系还在原来的位置。
第二种是:合自则害校八厚察续改翻用G50设定坐标系,对刀后将刀移动到G50设定的位置才能加工。对刀时先对基准刀,其他刀的刀偏都是相对于基准刀的。
第三种方法是MDI参数,运用G54~G59可以设定六个坐标系,这种坐标希晶差系是相对于参考点不变的,与刀具无关。这种方品激唱实临千山果法适用于批量生产且工件在卡盘上有固定装夹位置的加工。
航天数控系统的工件坐标系建立是通过G92 Xa zb
(类似于FANUC的G50)语句设定刀具当前所在位置的坐标值来确定。加工前需要先对刀,对刀首先对的是基准刀,对刀后将显示坐标清零,对其他刀时将显示的坐标值写入相应刀补参数。然后测量出对刀直径Фd,将刀移动到坐标显示X=a-d
Z=b 的位置,就可以运行程序了(此种方法的编程坐标系原点在工件右端面中心)。在加工过程中按复位或急停健,可以再回到设定的G92
起点继续加工。但如果出意外如:X或Z轴无伺服、跟踪出错、断电等情况发生,系统只能重启,重启后设定的工件坐标系将消失,需要重新对刀。如果是批量生产,加工完一件后回G92起点继续加工下一件,在操作过程中稍有失误,就可能修改工件坐标系,需重新对刀。鉴于这种情况,我们就想办法将工件坐标系固定在机床上。我们发现机床的刀补值有16个,可以利用,于是我们试验了几种方法。
第一种方法:在对基准刀时,将显示的参考点偏差值写入9号刀补,将对刀直径的反数写入8号刀补的X值。系统重启后,将刀具移动到参考点,通过运行一个程序来使刀具回到工件G92起点,程序如下:
N001 G92 X0 Z0;
N002 G00 T19;
N003 G92 X0 Z0;
N004 G00 X100 Z100;
N005 G00 T18;
N006 G92 X100 Z100;
N007 M30;
程序运行到第四句还正常,运行第五句时,刀具应该向X的负向移动,但却异常的向X、Z的正向移动,结果失败。分析原因怀疑是同一程序调一个刀位的两个刀补所至。
第二种方法:在对基准刀时,将显示的与参考点偏差的Z值写入9号刀补的Z值,将显示的X值与对刀直径的反数之和写入9好刀补的X值。系统重启后,将刀具移至参考点,运行如下程序:
N001 G92 X0 Z0;
N002 G00 T19;
N003 G00 X100 Z100;
N004 M30;
程序运行后成功的将刀具移至工件G92起点。但在运行工件程序时,刀具应先向X、Z的负向移动,却又异常的向X、Z的正向移动,结果又失败。分析原因怀疑是系统运行完一个程序后,运行的刀补还在内存当中,没有清空,运行下一个程序时它先要作消除刀补的移动。
第三种方法:用第二种方法的程序将刀具移至工件G92起点后,重启系统,不回参考点直接加工,试验后能够加工。但这不符合机床操作规程,结论是能行但不可行。
第四种方法:在对刀时,将显示的与参考点偏差值个加上100后写入其对应刀补,每一把刀都如此,这样每一把刀的刀补就都是相对于参考点的,加工程序的
G92起点设为X100 Z100,试验后可行。这种方法的缺点是每一次加工的起点都是参考点,刀具移动距离较长,但由于这是G00 快速移动,还可以接受。
第五种方法:在对基准刀时将显示的与参考点偏差及对刀直径都记录下来,系统一旦重启,可以手动的将刀具移动到G92 起点位置。这种方法麻烦一些,但还可行。
修改
根据刀具的实际参数和位置,将刀尖圆弧半径补偿值和刀具几何磨损补偿值输入到与程序对应的存储位置。如试切加工后发现工件尺寸不符合要求时,可根据零件实测尺寸进行刀偏量的修改。例如测得工件外圆尺寸偏大 0.5mm ,可在刀偏量修改状态下,将该刀具的 X 方向刀偏量改小 0.25mm。